Versatile materials
A history of plastics in automotive engineering
A guest post by
Dennis Kottmann*
Reading Time: 3 min
Related Vendors
Plastics are a popular material in automotive engineering due to their lightweight and lower cost. The lower strength compared to metals can be compensated for by using high-performance polymers or combining plastics with glass or carbon fibres. The components are manufactured using injection moulding.
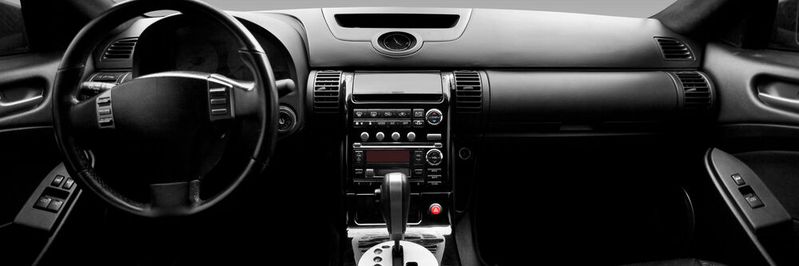
(Source: © Superstar/Shutterstock.com)
Plastics have been around for longer than cars. The first thermoplastic, called Parkesine, was presented by Alexander Parkes at the 1862 World Exhibition in London. It was a further developed cellulose nitrate on a natural basis and was intended to replace ivory. In 1886, more than twenty years later, Carl Benz presented the first car, the Benz Patent-Motorwagen Nummer 1( patent motorcar no. 1). It was made of wood and metal.
Plastic finally gained acceptance during the Second World War, when steel was heavily rationed. In 1941, Henry Ford tried to manufacture a car entirely out of plastics. It took another ten years to reach serial production. Since the production of the Ford Model T in 1951, plastic has been found in cars all over the world.
Plastics vs. metals
Besides metals, plastics are a widely used material in cars. Plastics are lighter, reducing the overall weight of the car and thus the fuel consumption. They are also less expensive and more corrosion-resistant than metals. The injection moulding process allows complex shapes to be produced in a single production cycle.
However, plastics have a major disadvantage compared to metals: their mechanical, chemical, and thermodynamic strength is lower. To increase this strength, there are various options available. Nowadays, there are numerous technical high-performance polymers, such as polyetheretherketone (PEEK). PEEK has high temperature and chemical resistance and is therefore suitable for seals, valves, or electrical components.
Another way to increase strength is to combine plastics with materials that have better mechanical properties. When the filling material reaches a volume fraction of up to 85 percent, it is called highly filled plastics. If the filling material is made up of fibres, the polymers are called fibre-reinforced. If the fibres are several millimetres long, the composite is called long fibre-reinforced thermoplastics (LFRT). Typical long filler fibres are glass or carbon fibres.
Examples of plastics in cars
A popular plastic used in car interiors is polycarbonate (PC). PC is transparent and is used for switches and instrument panels. Polyurethane (PU) is often used for seat cushions, armrests, and door panels. It is soft, flexible, and comfortable, has good abrasion resistance, and can be produced in various colours and textures.
A high proportion of glass fibres in polypropylene (PP) improves the toughness and strength of the components. It is often used for interior applications such as dashboards, door panels, and seat frames or in body components. Carbon fibre-reinforced polyamide (PA) has high tensile strength and is temperature-resistant. Therefore, it is particularly suitable for applications in the engine compartment, such as air filter housings.
LFRT manufacturing by injection melding
In the direct process, the filling fibres are introduced into the plastic melt immediately before the injection moulding process. This allows for individually adjustable fibre length, proportion, and material combination for each component, depending on the application challenge. The mixing process of polymer and fibre is called compounding. The difficult part is maintaining fibre length, as the mechanical benefits are lost if the fibres break before the component is created. Any waste can be processed internally into granulate and reused. This is called pre-consumer recycling.
* Dennis Kottmann is the Marketing Director of Surplex.
(ID:49510922)